20 Go-to Methods for Accurately Estimating Project Costs
Navigating the complexities of project cost estimation just got easier with this comprehensive guide packed with expert-backed methods. From leveraging technology to understanding market trends, discover the proven strategies to achieve accurate financial projections. Delve into the insights of seasoned professionals and master the art of precise cost evaluation.
- Combine Bluebeam And Buildxact
- Use Site Inspections And Historical Data
- Employ Detailed Assessment And Technology
- Utilize Custom Estimation System
- Understand Customer Needs And Site Details
- Price HVAC Jobs With Load Calculation
- Evaluate Cost Breakdowns And Market Prices
- Walk Projects With Team
- Research Market Trends And Pricing Data
- Use Square Foot Method
- Perform Detailed Line-Item Breakdown
- Thoroughly Research And Analyze All Aspects
- Segment Project Into Measurable Phases
- Adopt Granular Approach For Cost Breakdown
- Itemize Every Aspect Of The Project
- Review Plans And Designs Thoroughly
- Appraise Equipment And Analyze Market Trends
- Draft Detailed Breakdown Of Variables
- Research Construction Process Thoroughly
- Conduct Thorough Research And Analysis
Combine Bluebeam And Buildxact
In the fast-paced world of American construction, accurate cost estimation is the difference between a profitable job and a financial headache. Over the years, I've refined my approach to make sure my estimates are spot-on. It's all about combining the right tools with a clear, methodical process and it's saved me (and my clients) from costly mistakes time and time again.
Here's how I do it.
When it comes to estimating, two tools are always in my toolbox: Bluebeam and Buildxact.
Bluebeam is a game-changer for take-offs. I can mark up PDF plans quickly and extract detailed quantities, down to the last cubic meter of concrete or kg of reinforcement. This ensures nothing gets missed.
Then I use Buildxact to pull it all together. It's perfect for the American market because it links my quantities to real-time supplier pricing. That means if concrete prices increase or steel reinforcement fluctuates, I'm not caught off guard it's all reflected in the estimate.
Recently, I was working on an estimate for a project in New York involving concrete foundations. Using Bluebeam, I carefully reviewed the plans and discovered a discrepancy between the structural drawings and the general notes an extra 40m3 of concrete for the footings had been overlooked in the initial calculations.
From there, I plugged the updated quantities into Buildxact and saw that concrete prices had recently risen due to high demand. Adjusting for this increase, I updated the estimate to reflect the additional concrete and higher costs.
By identifying these issues early, I avoided what could have been a $10,000 mistake. Without the extra concrete accounted for, the project might have faced delays and cost blowouts once construction was underway. Instead, the builder and client appreciated the accuracy and transparency of the revised estimate.
This method isn't just about using software it's about having a system that's thorough and adaptable. Bluebeam ensures no detail is missed, and Buildxact keeps pricing realistic and current. Combine that with careful plan analysis and experience, and you're set up for success.
At the end of the day, it's not just about the numbers it's about delivering on promises, staying within budget, and keeping everyone on the same page. With the right approach, that's a goal every estimator can achieve.
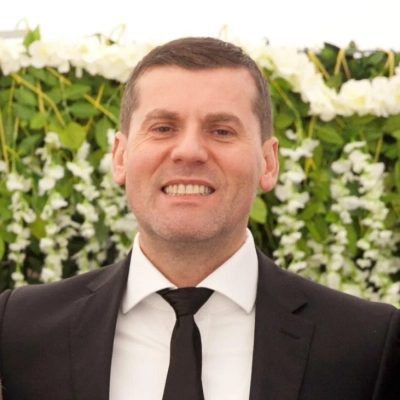
Use Site Inspections And Historical Data
My preferred method is combining thorough site inspections with historical cost data from similar projects. I think site inspections are often underappreciated, but they've saved my team from significant miscalculations. For example, on a large siding replacement project, an inspection revealed improperly installed insulation that was causing moisture damage beneath the panels. Because we had previously handled a project with nearly identical issues, we used those costs as a reference and added $8,000 to the initial estimate. This saved us from under-budgeting, and the client appreciated the upfront transparency.
For me personally, this approach ensures estimates are realistic and grounded in actual conditions, not just standard rates or assumptions. I also believe involving the team in the process enhances accuracy. During that siding project, our estimator and lead installer worked together to refine the numbers, reducing our margin of error to less than 3%. I've found that combining field experience with data is the best way to set the stage for a successful and profitable project.
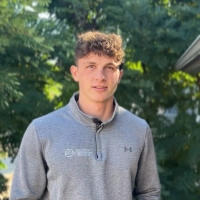
Employ Detailed Assessment And Technology
Accurately estimating project costs in construction requires a combination of experience, precise data, and the use of reliable tools. At C.D. Roofing & Construction Ltd., our go-to method involves a three-step approach: detailed assessment, leveraging technology, and contingency planning.
1. Detailed Assessment
We start with an on-site inspection, evaluating every aspect of the project. This includes measuring dimensions, assessing the condition of the existing structure, and identifying potential problem areas like water damage or ventilation issues. The key is not to rush this process—taking the time to document and photograph everything ensures no detail is overlooked.
2. Leveraging Technology
We use advanced estimating software that integrates with drone inspections and satellite imagery for precise measurements. This not only saves time but also eliminates human error in calculating roof dimensions or material quantities. We also input up-to-date material costs and labor rates to create a comprehensive and realistic estimate.
3. Contingency Planning
We include a contingency budget in every estimate, typically around 10-15%, to account for unexpected issues like structural repairs or weather-related delays. This practice ensures clients aren't blindsided by additional costs and allows us to maintain profitability while meeting their expectations.
Specific Example: Avoiding a Costly Mistake
One project that stands out was a large-scale roof replacement for a commercial property. During our initial assessment, we noticed subtle signs of moisture near the edge of the roof, which could easily have been dismissed. By using thermal imaging during the inspection, we identified extensive hidden water damage beneath the insulation layer. Without this step, the damage would have gone unnoticed until the project was underway, leading to delays, additional costs, and a frustrated client.
Because of our meticulous process, we revised the estimate to include the necessary repairs upfront, ensuring the project stayed on budget and on schedule. The client appreciated the transparency and professionalism, which reinforced our reputation as a trusted roofing partner.
This method ensures that every project is approached with accuracy, efficiency, and a commitment to delivering exceptional results.
Utilize Custom Estimation System
Hello,
Thank you for the opportunity to contribute to your article on accurately estimating project costs in construction. At SnapADU (https://snapadu.com/), a design-build firm specializing in accessory dwelling units (ADUs) in Southern California, we rely on a custom estimation system built in Excel and integrated with data exports from our project management software, Buildertrend.
Our method ensures accuracy by separating the takeoff process of quantifying the project's requirements from how we manage scopes and purchase orders. For example, entering a single field, such as kitchen size, automatically updates related purchase orders, including cabinetry, countertops, and fixtures. This system embeds rules and formulas, significantly reducing human error while streamlining calculations.
In a recent project, a kitchen size adjustment during the design phase triggered automatic recalculations across multiple purchase orders. This saved us from underordering materials, avoiding costly delays and ensuring our budget remained accurate. Without this system, manual updates could have introduced errors, causing significant overruns.
Our approach combines efficiency, accuracy, and scalability, allowing us to deliver projects on time and within budget. I'd be happy to provide additional details or examples if needed!
Warm regards,
Whitney Hill
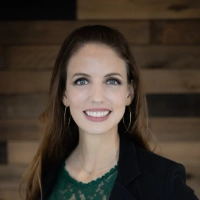
Understand Customer Needs And Site Details
When it comes to accurately estimating project costs in construction, the key is thoroughness and attention to detail. At New York Gates, we always start by really understanding the customer's needs and the unique aspects of the site. This means carefully evaluating things like the type of gate required, the material, the level of customization, and even the surrounding environment. From there, we take precise measurements and use our extensive industry knowledge to put together an accurate, transparent estimate.
This approach paid off during a commercial project for a large warehouse. The client needed a heavy-duty gate for frequent use, but initial plans underestimated the reinforcement needed for their wall setup. By reviewing every detail upfront and consulting with our technicians, we caught the issue and adjusted the design and cost estimate before installation even began. It saved the client both time and unnecessary expenses, and they were beyond pleased with the result. At the end of the day, it's all about doing the groundwork to deliver what's best for the customer!
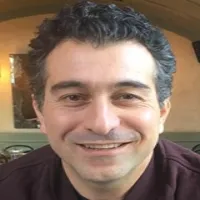
Price HVAC Jobs With Load Calculation
I price HVAC jobs from load calculation and material takeoff, factoring in labor, equipment, ductwork, and contingencies. My recent commercial HVAC project operated under my pricing scheme; a faulty gauge was discovered against estimated labor hours, based upon duct runs being more complicated than necessary. Adjusting the estimate prior to the start of the project saved the company (and the customer) $7,000 in overage. I'd rather have someone upset with something I can control than blindsided by what I can't; my customers should never be blindsided.
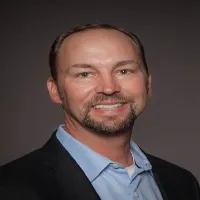
Evaluate Cost Breakdowns And Market Prices
The method I use for estimating the cost of a construction project involves cost breakdowns of previous projects and the current market price. I carefully evaluate labor, materials, and equipment costs as well as contingency. For example, on my last job, one of my subcontractors provided an excessively low material estimate. After reviewing material breakdowns of the previous projects I've worked on, I found that it was a low breakdown because it did not account for the delivery fee. Therefore, I was able to bring this to the attention of the subcontractor, who provided a more general material estimate to avoid a cost overage and an unknown adjustment of $10,000 later. This helps facilitate proper budgeting without any unknowns.
Walk Projects With Team
My go-to method for accurately estimating construction project costs is to personally walk the proposed project with my team to gather all necessary details. This hands-on approach ensures we capture accurate measurements, assess potential challenges, and fully understand the project scope. We then input this information into our job estimate workbook, which incorporates inputs from previous projects, including costs and profit margins. Over time, refining these numbers has allowed us to competitively bid on every project within our sphere of expertise.
For example, using this workbook on a recent project, we identified discrepancies in subcontractor quotes compared to historical data. This helped us negotiate more favorable rates, staying competitive without sacrificing quality. A well-maintained estimate system ensures accuracy and confidence in every bid.
Research Market Trends And Pricing Data
My go-to method for accurately estimating project costs in construction is by conducting thorough research and analysis of the current market trends and pricing data. This involves looking at similar projects in the same location, considering material and labor costs, and factoring in any potential external factors that may impact the cost.
One specific example where this method helped me avoid a costly mistake was when I was working on a commercial building project. My client wanted to cut costs by using cheaper materials, but after my research, I found out that the location where the building was being constructed had recently undergone zoning changes that required all buildings to meet certain energy efficiency standards.
If we had gone ahead with the cheaper materials, it would have resulted in costly changes and delays during the construction process to meet these standards. By using my research method, I was able to accurately estimate the cost with the necessary materials, preventing any costly mistakes for my client. Additionally, by staying up-to-date with market trends and pricing data, I was able to negotiate better prices with suppliers and contractors, further saving costs for my client.
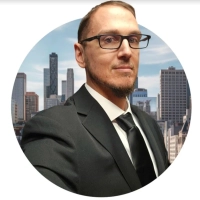
Use Square Foot Method
Accurate estimation of project costs in construction is an essential part of my job. It not only helps me to provide accurate information to my clients but also enables me to avoid costly mistakes. One method that I have found to be particularly effective in estimating project costs is the square foot method. This method involves calculating the total cost of a project by multiplying the square footage of a property by a predetermined cost per square foot.
For example, I had a client who was interested in purchasing a commercial space for their business. They wanted to renovate the space and turn it into a retail store. Using the square foot method, I was able to estimate the renovation costs accurately by taking the square footage of the space and multiplying it by the average cost per square foot for similar retail stores in the area.
This helped my client avoid a costly mistake of underestimating the renovation costs and potentially overspending on their budget. By using this method, I was able to provide them with a realistic estimate and negotiate a fair price for the property.
Perform Detailed Line-Item Breakdown
My go-to method is a detailed line-item breakdown, combined with historical cost data from similar projects. I start by identifying every component-labor, materials, permits, and contingencies-then cross-check prices using updated supplier quotes and industry benchmarks. Including a 10-15% buffer for unforeseen expenses ensures the estimate remains realistic.
In one project, this method flagged an unusually low supplier quote for specialized piping. After double-checking, we discovered it was a pricing error. Correcting it before submitting the bid saved us from losing money on the job. Breaking down costs in detail not only ensures accuracy but also provides transparency, making it easier to justify estimates to clients and adjust if necessary.
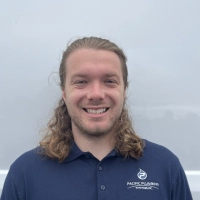
Thoroughly Research And Analyze All Aspects
Accurately estimating project costs in construction is an essential skill that I have honed over the years. My go-to method for this task involves thoroughly researching and analyzing all aspects of the project, from materials and labor costs to potential unforeseen factors.
One specific example where this method proved to be invaluable was during a renovation project for a client's residential property. The initial estimate provided by the contractor seemed reasonable, but upon further inspection, I noticed that there were no provisions for potential delays or complications due to weather conditions.
Based on my experience with similar projects in the past, I knew that weather could significantly affect construction timelines and add additional costs. Therefore, I advised my client to include a contingency budget in the estimate to account for any potential delays.
Sure enough, halfway through the project, heavy rainstorms caused significant delays, and without the contingency budget, the project would have gone over budget. Thanks to my thorough research and analysis of all factors involved, we were able to avoid a costly mistake and complete the project within budget.
This experience further solidified my belief in always taking a comprehensive approach when estimating project costs in construction. It's not just about looking at material and labor costs; it's about considering all potential variables that could impact the project and being prepared for them.
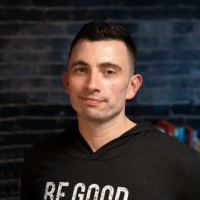
Segment Project Into Measurable Phases
I believe the most effective method for estimating project costs is to segment the project into smaller, measurable phases and assign costs to each phase based on current market rates. In my experience, breaking down tasks ensures no step is overlooked and creates transparency when allocating budgets. For example, during a system overhaul for automating customer onboarding, we divided the project into six phases: design, development, testing, deployment, training, and maintenance. By evaluating each phase separately, we identified that 25% of the budget would be needed for post-launch maintenance, an area often underestimated. This phased approach kept the project within a 3% margin of the original budget.
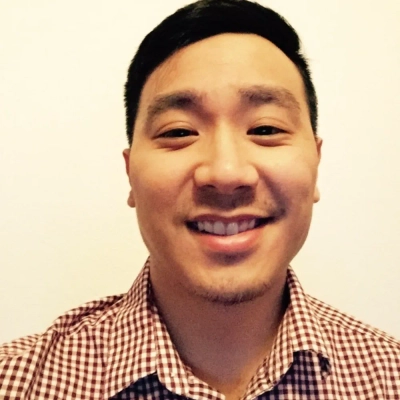
Adopt Granular Approach For Cost Breakdown
My go-to method for accurately estimating project costs in construction is a detailed, line-by-line breakdown—what I call the 'granular approach.' I don't just look at the big-ticket items; I dive into every detail, from materials and labor to small items like permits and unforeseen contingencies.
I remember a project early in my career where we were building a commercial space. The initial estimate seemed solid, but I wasn't feeling 100% confident, so I decided to review every single cost. During that review, I realized we had underestimated the electrical wiring cost by a significant margin because we hadn't accounted for the higher-spec materials the client wanted.
Catching that early saved us a lot of headaches. Instead of scrambling to explain the unexpected costs midway through, we adjusted the estimate before finalizing the contract, and the client appreciated the transparency. It also helped maintain trust when we had to adjust the scope slightly due to other unanticipated costs.
This method takes more time upfront, but it's always worth it. By breaking things down thoroughly, I can avoid those 'hidden costs' that can spiral into bigger problems down the line.
Itemize Every Aspect Of The Project
My go-to method for accurately estimating project costs in construction is the detailed cost breakdown approach. This involves itemizing every aspect of the project-materials, labor, equipment, and overhead-into a comprehensive spreadsheet. By analyzing historical data and current market rates, I can create a realistic budget that reflects the true scope of the project.
A specific example of this method's effectiveness occurred during a commercial renovation project. Initially, I estimated costs based on rough averages, but upon conducting a detailed breakdown, I discovered that the price of specialized materials had significantly increased. This insight allowed me to adjust the budget and negotiate with suppliers ahead of time, ultimately saving the project from a potential budget overrun of over 15%. This meticulous approach not only prevented costly mistakes but also instilled confidence in stakeholders regarding our financial planning.
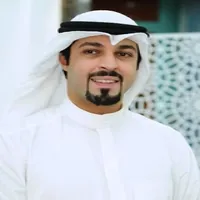
Review Plans And Designs Thoroughly
Before any construction begins, I make sure to review all plans and designs, taking into consideration every detail from materials and labor costs to any potential permits or fees that may be required. By having a deep understanding of the project scope, I can establish a realistic budget and foresee any possible issues that may arise during the construction process.
One specific example where this method has helped me avoid a costly mistake was during a commercial build-out for a new business in my town. The initial plans had estimated the cost of materials to be significantly lower than what they actually ended up being. However, by carefully reviewing the plans and understanding the specific materials needed for the project, I was able to accurately estimate the true cost and adjust the budget accordingly.
This not only helped me avoid a costly mistake for my client but also ensured that the project stayed within budget and on track for completion. It’s always important to be thorough when estimating project costs in construction, as even small miscalculations can have a significant impact on the overall success of a project.
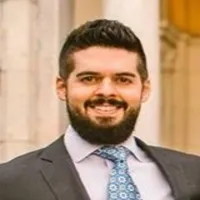
Appraise Equipment And Analyze Market Trends
My go-to method for accurately estimating project costs in construction involves a combination of detailed equipment appraisals and market trend analysis. Understanding the current value and expected depreciation of equipment plays a significant role in creating realistic budgets. We also factor in maintenance costs and availability to ensure that every piece of machinery contributes to the overall project efficiency.
One time we had a project involving a construction company planning to expand their fleet for a large-scale infrastructure job. During the appraisal process, we uncovered that several pieces of used equipment they intended to purchase had significant maintenance needs that weren't reflected in the seller's asking price.
Our detailed analysis allowed the client to negotiate better terms and allocate part of their budget toward more reliable alternatives. This saved them from potential downtime and unplanned repair costs, which could have derailed their project timeline.
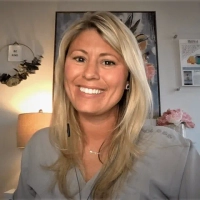
Draft Detailed Breakdown Of Variables
As someone working for a company that finances various industries such as construction, we first draft a detailed breakdown of all the variables involved in a project. It can be materials, labor, equipment, and potential risks. Creating a clear scope of work and estimating each line item separately helps paint a more accurate picture. It's easy to overlook smaller costs, like transportation or disposal fees, but including everything upfront helps prevent surprises.
A specific instance comes to mind where we were working with a client in construction, and I was involved in estimating costs for a large equipment acquisition. Initially, there was a push to cut costs by choosing lower-quality machinery. However, my method of detailed cost estimation revealed that the long-term maintenance and downtime would cost far more than the initial savings on cheaper equipment. This insight helped avoid a costly decision, and the client opted for higher-quality machinery that ultimately saved them in the long run.
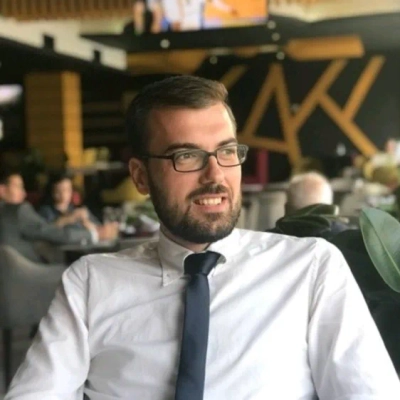
Research Construction Process Thoroughly
Over the years, one of the most valuable skills I've honed is the ability to accurately estimate construction project costs. This is an essential aspect of my job as it allows me to provide accurate information and guidance to my clients, whether they are buying or selling a property.
My go-to method for estimating project costs involves thoroughly researching all aspects of the construction process. This includes understanding current market conditions, materials and labor costs, as well as any potential delays or unforeseen expenses that may arise during the project. Additionally, I always consult with experienced contractors and builders to get their input on the estimated costs.
One specific example where this method helped me avoid a costly mistake was when I was working with a client who wanted to renovate their newly purchased commercial property. They had received an estimated cost from the contractor they were planning to hire, but upon further research and consultation with other professionals, it became clear that the estimate was significantly lower than the actual costs.
By utilizing my go-to method for estimating project costs, I was able to provide my client with a more accurate estimation and also advise them on negotiating better terms with the contractor. This ultimately saved my client thousands of dollars in unexpected expenses and allowed them to make informed decisions about their investment.
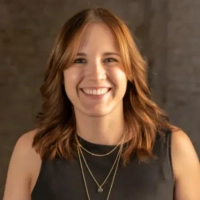
Conduct Thorough Research And Analysis
My go-to method for estimating project costs is conducting thorough research and analysis. I gather information on current market prices for materials, labor costs, and any potential hidden expenses that may arise during the project. This includes taking into account any external factors such as location, seasonality, and availability of resources.
One specific example where this method proved to be crucial was when I was working with a client who wanted to renovate their newly purchased commercial property. They had received a rough estimate from a contractor, but I knew it was important to have a more detailed and accurate cost breakdown. After conducting my research and analysis, I was able to identify potential hidden costs such as obtaining necessary permits and unexpected structural issues in the building.
By presenting my client with a comprehensive cost estimate, they were able to make an informed decision about moving forward with the project. It also helped us avoid any costly surprises or setbacks during the renovation process.
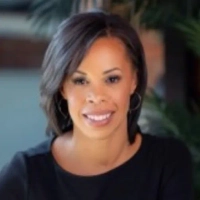