6 Impacts of Prefabrication and Modular Construction On Projects
Imagine revolutionizing your construction projects with cutting-edge techniques that promise speed and quality. Hear from industry leaders like CEOs and Managing Members who have successfully integrated prefabrication and modular construction into their workflows. This article begins with insights on how these innovations enhance speed and quality and concludes with strategies to achieve consistent quality in housing developments. Discover six expert insights that can transform your approach to construction.
- Speed and Quality Enhanced
- Streamlined Building Process
- Improved Accuracy and Resilience
- Enhanced Efficiency and Safety
- Consistent Quality in Housing Developments
- Expedited Installation and Reduced Waste
Speed and Quality Enhanced
In my experience, prefabrication and modular construction have been game-changers. For example, I've seen hospitals go up in just a week using modular methods—something that would've taken months traditionally. The speed is unreal, and the quality doesn't suffer because everything's built in a controlled environment.
Another big win is cost-savings. Sure, the upfront investment might be a bit higher, but you save so much in labor and materials down the road. Plus, it's way more sustainable—less waste, less disruption to the community, and safer for workers. It's a no-brainer for anyone looking to streamline their projects without sacrificing quality or safety.
Streamlined Building Process
As the founder of RG ProBuilders, I've seen how prefabrication and modular construction streamline the building process, particularly in the unpredictable climates of areas like Phoenix. Our ModPods are a prime example. They accept modular design by offering customizable, luxury living options that simplify logistics and reduce waste.
In one memorable project, we used our ModPods to build multiple units simultaneously. This approach not only cut construction time significantly but also minimized site disruption. By prefabricating key components, we maintained quality control while offering homeowners custom solutions that meet both aesthetic and functional needs.
The benefit is clear: faster delivery and less material waste mean reduced costs for homeowners without sacrificing quality. Our ModPods can be fully set up more rapidly than traditional builds, providing families with highly functional, expandable living spaces that are ready to be enjoyed much sooner. This modular approach has redefined what our clients envision for personal living spaces.
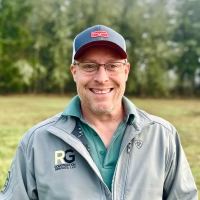
Improved Accuracy and Resilience
Prefabrication and modular building have added an entirely new degree of accuracy to our exterior work, so that we can build custom-fit pieces with far less improvisation on the job site. One of our recent projects where this strategy came into play was a sophisticated siding job for a multi-level house with distinct design corners. Our modular panels were custom-built to the exact size and angles we needed, instead of each one being cut by hand on-site. That accuracy shaved out unnecessary waste, shortened the time for installation, and ultimately created a clean, polished look that would have been much more difficult without it.
The most unexpected advantage is the heightened resilience and resistance to weather conditions of the pre-engineered materials. Because they're produced under a controlled environment, these materials are better treated and better sealed to ensure they are less susceptible to warping or weathering. This level of controlled quality has enabled us to produce exteriors that last in the elements and in the worst weather conditions, which has enabled us to confidently provide longer warranties.
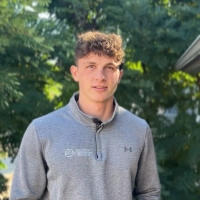
Enhanced Efficiency and Safety
Prefabrication and modular construction have significantly impacted our projects by enhancing efficiency, quality, and safety. For example, in a recent multi-unit residential project, we employed modular prefabrication for electrical panels and conduit assemblies. This approach allowed us to pre-assemble complex components in a controlled environment, reducing on-site labor time and minimizing disruptions to other trades.
The benefits were notable: installation time was cut by nearly 30%, and we saw fewer errors compared to traditional methods. The controlled conditions of prefabrication also meant higher quality standards, resulting in fewer reworks. This successful implementation showcases how prefabrication can streamline workflows and deliver consistent, high-quality results for our clients.
Have you seen similar benefits with prefabrication in your own work, or are you considering incorporating it into future projects?
Another advantage we noticed was improved site safety. By reducing the amount of work done on-site, we minimized the exposure of our team to potential hazards like working at height or in confined spaces. Prefabrication also meant less clutter and material handling on-site, contributing to a cleaner, safer work environment.
From a scheduling perspective, prefabrication helped us maintain a predictable timeline, even in challenging conditions. Weather delays, which often impact traditional construction, had minimal effect on the project since much of the work was completed off-site. This approach not only saved time but also helped manage costs more effectively, as we faced fewer delays and unexpected expenses.
Overall, the experience has encouraged us to look for more opportunities to integrate prefabrication and modular approaches into future projects. They offer tangible benefits for efficiency, quality, safety, and cost-effectiveness—aligning perfectly with our goal of delivering the best possible service to our clients.
Are there any specific projects you're considering that could benefit from this approach? I'd be happy to share more insights based on our experiences.
Consistent Quality in Housing Developments
In our manufactured housing developments, we've started using prefab sections for porches and add-on rooms, which has been incredible for maintaining consistent quality. Just last quarter, we completed a 24-unit addition to one of our communities in half the expected time by using pre-built components instead of traditional construction methods. While the upfront costs were about 15% higher, we saved significantly on labor and got tenants in faster, making the investment totally worth it.
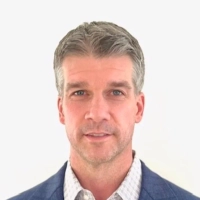
Expedited Installation and Reduced Waste
The shift towards prefabrication and modular construction has significantly influenced the development and deployment of Oziflow's rainwater-harvesting solutions. Our super-slim, modular tanks are designed for easy integration into both new builds and existing structures, aligning seamlessly with the streamlined processes of modern construction projects. For example, in a recent project involving a new residential community, our Oziflow systems were prefabricated and then installed in stages to coincide with the site's development schedule. This modular approach not only expedited the installation process but also reduced on-site labor costs and minimized construction waste. The adaptability of our tanks to various architectural designs and constraints further exemplifies the practical benefits of modular construction, allowing for enhanced water conservation and sustainability in urban planning. This strategy has enabled us to significantly expand our market reach, reduce environmental impact, and deliver tailored solutions that meet specific client needs more efficiently.