7 Effective Training Techniques for Construction Safety
Discover cutting-edge techniques to elevate construction safety training, each endorsed by seasoned industry experts. This article demystifies the blend of traditional methods and innovative tech-driven approaches to foster a safer workplace. Insights include practical applications ranging from hands-on simulations to multimedia learning strategies.
- Implement 'Shadow & Lead' for Hands-On Safety
- Blend Toolbox Talks with Interactive Simulations
- Simulate Real-World Risks for Practical Learning
- Combine Orientation, Site Training, and Drills
- Mix On-Job Practice with VR Scenarios
- Utilize Multimedia Approach for Visual Learners
- Prioritize Hands-On Training with Safety Checklists
Implement 'Shadow & Lead' for Hands-On Safety
At C.D. Roofing & Construction Ltd., training new employees and subcontractors on construction safety procedures is a top priority. My preferred method is a hands-on, mentorship-based approach that combines formal safety training with on-site demonstrations and real-world application. Roofing is a high-risk trade, so ensuring that every team member understands and follows proper safety protocols is critical for both efficiency and job site security.
Effective Training Technique: The "Shadow & Lead" Method
One of the most effective techniques I've implemented is what I call the "Shadow & Lead" method:
1. Shadow Phase - New hires or subcontractors work alongside an experienced crew leader for the first few weeks, observing proper safety procedures in action. This includes PPE usage, ladder safety, fall protection, and proper material handling. Seeing these procedures done correctly in real time helps them retain the information far better than reading a manual alone.
2. Lead Phase - Once they've observed enough, they begin to perform tasks under supervision, applying what they've learned while the experienced crew member coaches and corrects them as needed. This ensures they build confidence while maintaining safety standards.
Additional Training Tools & Best Practices
- Regular Toolbox Talks - Before starting work each day, we hold quick 5-10-minute safety briefings to go over site-specific hazards, weather conditions, and equipment checks.
- Safety Checklists & SOPs - Every new employee gets a printed safety handbook covering fall protection, equipment use, and emergency procedures. Digital versions are also available via company tablets.
- Harness Fit & Fall Protection Drills - Since falls are one of the biggest risks in roofing, we have monthly fall protection drills where employees practice proper harness fitting and rescue procedures.
- Hands-On Equipment Training - Before using power tools or heavy equipment, every worker undergoes a certification process that includes both written knowledge and hands-on demonstrations.
Final Advice for Other Contractors
Training isn't just about meeting regulations--it's about creating a safety-first culture. When employees understand the "why" behind each procedure, they're more likely to follow it consistently. Investing in hands-on mentorship, real-time feedback, and ongoing safety reinforcement ensures that your team not only works efficiently but also goes home safely at the end of each day.
Blend Toolbox Talks with Interactive Simulations
A highly effective method for training new employees or subcontractors on construction safety procedures is a combination of hands-on training and digital reinforcement. One specific technique that works well is the "Toolbox Talk + Interactive Simulation" approach:
Daily Toolbox Talks - Start each workday with a 5-10 minute safety briefing focused on site-specific hazards and best practices. This keeps safety top of mind and ensures everyone understands the risks before starting work.
Interactive Hazard Simulations - Use virtual reality (VR) safety training or interactive scenario-based e-learning modules. These tools immerse workers in real-life hazard situations, teaching them how to react appropriately. Even if VR isn't an option, videos and hands-on demonstrations can reinforce key safety protocols effectively.
Mentorship & On-the-Job Training - Pair new workers with experienced team members to provide guidance, answer questions, and ensure safety practices are followed in real time.
Testing & Certification - Require short quizzes or practical assessments to confirm understanding before allowing workers on hazardous job sites.
This blended approach ensures both theoretical knowledge and practical application, reducing the risk of accidents and improving long-term safety culture on the job site.
Simulate Real-World Risks for Practical Learning
Keep it real and hands-on. No one learns safety from a PowerPoint.
I throw them straight into practical, on-site training. Harness on, gear checked, real-world scenarios. We simulate common risks, like an unexpected fall or improper equipment use, so they feel what could go wrong and learn how to react.
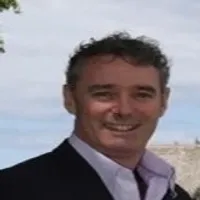
Combine Orientation, Site Training, and Drills
The best method for training new employees or subcontractors on construction safety procedures is a combination of hands-on training, interactive learning, and continuous reinforcement. Here's a structured approach that works effectively:
1. Onboarding Safety Orientation
Conduct a mandatory safety orientation on the first day.
Cover key OSHA (or local regulatory) safety standards.
Provide a safety handbook with company policies and emergency procedures.
Use videos and real-world case studies to demonstrate hazards and best practices.
2. Site-Specific Safety Training
Conduct walkthroughs of active job sites to explain specific hazards.
Demonstrate PPE (Personal Protective Equipment) usage and ensure proper fit.
Assign a mentor or experienced team member to guide new workers.
3. Toolbox Talks & Daily Safety Huddles
Implement short, daily safety meetings (5-10 mins) before work starts.
Focus on a different safety topic each day (e.g., fall protection, electrical safety).
Encourage active participation with questions and real-world examples.
4. Hands-On & Scenario-Based Training
Use simulated emergency drills for fire, fall, or electrical hazards.
Implement "See it, Fix it, Report it" training where workers identify and correct hazards.
Use VR (Virtual Reality) or AR (Augmented Reality) simulations for high-risk tasks.
5. Safety Competency Tests & Certifications
Require employees to pass a basic safety test before starting work.
Offer certification programs (e.g., WHMIS, Working at Heights, Confined Spaces).
Maintain ongoing refresher training to reinforce key safety principles.
6. Incentives & Accountability
Implement a safety recognition program (reward teams with the best safety records).
Encourage peer-to-peer accountability--workers should feel responsible for each other's safety.
Use incident reviews as learning opportunities without blame.
Best Tool for Safety Training:
One highly effective tool is Learning Management Systems (LMS) like ClickSafety or iHasco, which provide interactive, trackable safety courses for workers. This ensures compliance and allows for progress tracking.
Mix On-Job Practice with VR Scenarios
When training new folks, I blend hands-on practice with VR simulations. Start by pairing them with experienced crew members to tackle real tasks--nothing beats learning on the job. Then, we jump into VR scenarios that mimic tricky situations, like handling equipment malfunctions or navigating fall risks. It's like a safety sandbox--mess up here, and no one gets hurt. This mix builds muscle memory and confidence fast. Regular check-ins and quick quizzes keep everyone sharp without overloading them.
Utilize Multimedia Approach for Visual Learners
As the CEO and founder of Pacific Remodeling, I prioritize a multimedia approach to training new employees and subcontractors on construction safety procedures. Recognizing that many construction professionals are hands-on visual learners, we utilize safety videos, direct instruction, and practical demonstrations. Trainees then practice these scenarios under supervision, receiving constructive feedback to reinforce correct practices. This method aligns with industry best practices, which emphasize the effectiveness of combining visual aids with interactive learning to enhance engagement and retention.
Prioritize Hands-On Training with Safety Checklists
At GreenAce Lawncare, we prioritize hands-on safety training from day one. We use practical tools like safety checklists to ensure every team member understands and follows the correct procedures before starting any task. Our immersive training approach includes real-life scenarios to show the importance of safety, making it feel natural, not just procedural. Pairing new hires with experienced team members fosters a culture of mentorship, where safety is modeled and reinforced daily. This method has proven effective, as employees not only learn the rules but embrace them, creating a safer, more confident work environment.