How Lean Construction Reduces Waste and Improves Efficiency
Discover the transformative power of lean construction, a method revolutionizing the industry by slashing waste and boosting efficiency. This article unveils a series of innovative practices, validated by field experts, designed to optimize every stage of the construction process. Engage with the wisdom of seasoned professionals and embrace strategies that promise to elevate projects to new heights of operational excellence.
- Implement Just-In-Time Material Deliveries
- Use Just-In-Time Delivery for Plumbing
- Adopt Virtual Tours for Property Viewings
- Schedule Just-In-Time Material Deliveries
- Apply 5S Method for Job Sites
- Use Pull Planning in Scheduling
- Adopt Value Stream Mapping
- Streamline Production with Recycled Materials
- Reduce Inventory with Just-In-Time Delivery
- Optimize Material Orders with Digital Tracking
- Use Real-Time Project Management Tools
- Utilize Continuous Integration and Delivery
Implement Just-In-Time Material Deliveries
As a civil engineer with more than 15 years of experience in the construction industry, I've seen how lean construction principles can transform the way we work. One example that really stands out is from a project where we were building a complex of buildings in an urban area with a tight site with barely any room to spare. Space was at such a premium that we had to get creative to avoid inefficiencies.
We applied the "just-in-time" approach, aligning material deliveries with the project schedule. By also using value stream mapping, we identified areas where materials were being unnecessarily moved or stored, which wasn't adding value to the project. This allowed us to streamline the supply chain and coordinate deliveries so that materials arrived only when needed. The result was less clutter on-site, reduced transport costs, and a smoother workflow-all while minimizing waste, saving time and allowing for a safer workplace.
To take it a step further, we also implemented the Last Planner System to bring everyone on the same page. By involving subcontractors and suppliers in weekly planning meetings, we created a collaborative process where everyone could anticipate and resolve issues before they became problems. This not only improved coordination but also ensured that the work flowed smoothly, with fewer delays and rework.
The combination of these lean practices-value mapping, just-in-time deliveries, and the Last Planner System-helped us keep the site organized, safer and much more efficient. It was always rewarding to see how the construction processes really helped the project to run more smoothly and organized.
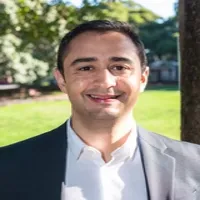
Use Just-In-Time Delivery for Plumbing
We've incorporated Just-In-Time (JIT) material delivery to align with lean construction principles, significantly reducing waste and improving efficiency. Instead of stockpiling materials at job sites, we coordinate deliveries to arrive as they're needed, based on project schedules.
For example, during a recent commercial plumbing project, we used JIT to ensure that pipes, fittings, and fixtures were delivered in phases aligned with each stage of the installation. This approach eliminated clutter on-site, reduced the risk of material damage or theft, and minimized the time spent searching for parts.
The benefits included a 20% reduction in material waste and improved workflow, as crews could focus on tasks without delays caused by missing or misplaced items. Lean practices like this not only optimize resources but also create a smoother, more predictable construction process.
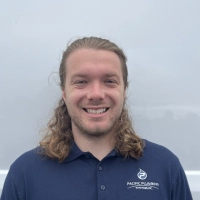
Adopt Virtual Tours for Property Viewings
A core principle of lean construction is the relentless pursuit of waste reduction and enhanced efficiency across every stage of a project. I have embraced several lean practices, which have delivered substantial benefits to both my clients and myself.
For instance, one of the common challenges I face as a real estate agent is managing multiple properties and clients simultaneously. In order to streamline this process and reduce unnecessary waste, I adopted the practice of using virtual tours for property viewings instead of physically taking clients to each property.
This not only eliminated transportation costs but also saved valuable time for both me and my clients. By utilizing technology in this manner, I was able to improve efficiency while also reducing waste in the form of transportation emissions.
Moreover, I have also implemented a lean practice of using electronic signatures for all necessary documents instead of printing and physically signing them. This has not only reduced paper wastage but has also resulted in faster and more efficient transactions with my clients.
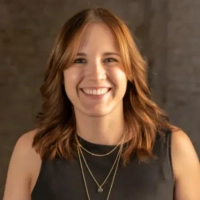
Schedule Just-In-Time Material Deliveries
We incorporate principles of lean construction by focusing on minimizing waste and maximizing value throughout every stage of a project. One practice we've implemented is just-in-time delivery of materials. By scheduling deliveries to arrive exactly when needed, we reduce excess inventory on-site, minimize material damage, and free up valuable workspace.
For example, during a recent renovation project, we worked closely with suppliers to coordinate deliveries based on the project timeline. This eliminated unnecessary stockpiling, improved workflow, and reduced carrying costs. The result was a more efficient process with fewer delays and less waste, which ultimately improved project profitability.
Apply 5S Method for Job Sites
We implement lean construction in residential construction via methods like 5S-Sort, Set in Order, Shine, Standardize, Sustain-in the job site. Everything has its place to prevent extra motion, and we've eliminated waiting during downtime. For example, one of my most recent projects saw a 15% increase in labor productivity due to this principle being applied and a reduction in materials going missing. A clean, orderly space is safe and helps reduce rework because my team can focus on the little things to make sure it gets done right the first time.
Use Pull Planning in Scheduling
Lean construction is a methodology that aims to maximize value and minimize waste in construction projects. It draws inspiration from lean manufacturing practices and focuses on continuously improving processes through the elimination of non-value adding activities.
One example of a lean practice that I have implemented is using pull planning in project scheduling. Pull planning involves engaging all stakeholders, including subcontractors and suppliers, at the beginning of a project to collaboratively develop a detailed schedule based on their expertise and capabilities. This allows for more accurate timelines and reduces delays caused by miscommunication or unexpected challenges.
As a result, I have seen significant improvements in project efficiency and reduction of waste. By involving all stakeholders in the planning process, there is better coordination and understanding of each party's responsibilities. This has led to fewer delays and rework, ultimately saving time and resources.
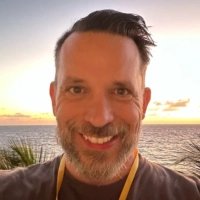
Adopt Value Stream Mapping
Incorporating lean construction principles has been a game-changer for improving efficiency and reducing waste in our projects. One key practice I've implemented is value stream mapping, which helps us identify and eliminate steps in the construction process that don't add value. I remember one project where we were consistently running into delays because materials would often arrive at the site late or out of order, causing stoppages.
To address this, we worked closely with our suppliers to streamline the delivery process. By mapping out the material flow and synchronizing deliveries with our schedule, we were able to ensure that the right materials arrived just in time, reducing inventory and eliminating the need for extra storage space on-site.
The result? We saw a significant reduction in downtime and better utilization of labor. Our project timeline improved by 15%, and we saved on storage and handling costs. This small change made a big impact in terms of efficiency and cost savings, and it's a practice I now incorporate in every project. Lean construction isn't just about cutting costs; it's about creating smarter, more efficient workflows that benefit everyone involved.
Streamline Production with Recycled Materials
At Make My Freshener, we incorporate principles of lean construction by focusing on reducing material waste and optimizing our production processes. One example is our commitment to using recycled paperboard for our custom air fresheners, which aligns with both efficiency and sustainability goals.
By streamlining our design and manufacturing workflow, we minimize excess material usage and energy consumption. For instance, our automated cropping feature ensures precise cuts for custom shapes, reducing waste from offcuts and scraps. This lean practice not only lowers our environmental impact but also improves cost efficiency, allowing us to offer competitive pricing while staying eco-friendly. The result is a win for both our business and the planet, as we create high-quality products with sustainability at the core.
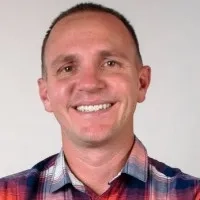
Reduce Inventory with Just-In-Time Delivery
Lean construction is a management philosophy that focuses on maximizing value and minimizing waste in the construction process. By implementing lean practices, I have not only been able to provide better service to my clients but also improve my overall productivity.
One example of a lean practice that I have implemented is just-in-time (JIT) delivery. This involves ordering materials and supplies only when they are needed, rather than stockpiling them in advance. By using JIT delivery, I have reduced excess inventory and storage costs while ensuring that materials are readily available when they are needed for a project. This has not only saved me money but also allowed me to be more efficient in completing projects on time.
Another lean practice that I have incorporated is value stream mapping. This involves analyzing the entire construction process and identifying areas of waste or inefficiency, then finding ways to eliminate or improve these areas. By using this method, I have been able to streamline my processes and reduce unnecessary steps, resulting in faster project completion and improved customer satisfaction.
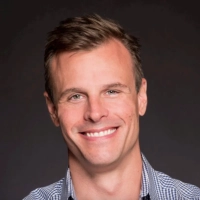
Optimize Material Orders with Digital Tracking
I have seen firsthand the importance of incorporating lean construction principles in reducing waste and improving efficiency in construction projects. One example of a lean practice that I have implemented is implementing just-in-time (JIT) delivery of materials to the construction site.
In the past, I have seen many projects suffer from delays and increased costs due to improper material management. With JIT delivery, we are able to minimize excess inventory on site and only order materials as needed, reducing waste and avoiding unnecessary storage costs.
One particular project where this practice was implemented saw significant benefits. The timeline for completion was reduced by 15%, resulting in cost savings for both my client and the contractor. Additionally, there were fewer errors in material ordering and handling, leading to a decrease in rework time and costs.
Moreover, implementing JIT delivery also allowed for better utilization of space on the construction site. This freed up more space for workers to move around, resulting in increased productivity and improved safety.
Use Real-Time Project Management Tools
Working with engineers and contractors on new developments has shown me how small changes in planning can reduce waste and improve efficiency. One example is optimizing material orders to match exact project needs instead of over-ordering. Builders often round up estimates to avoid running short, but this can lead to excess materials sitting unused. I have worked with contractors who use digital inventory tracking to refine their orders, cutting down on waste and keeping costs in check.
Miscommunication between teams can lead to delays and rework, which adds unnecessary costs. I was involved in a project where plumbing and electrical work overlapped, causing last-minute adjustments that could have been avoided with better scheduling. Since then, I have encouraged developers to use real-time project management tools to track progress and flag potential conflicts early.
Efficiency in construction benefits buyers, too. When projects stay on schedule and within budget, homes hit the market at competitive prices.
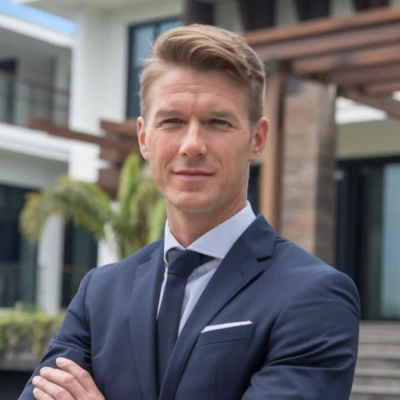
Utilize Continuous Integration and Delivery
At LinkedIn, while we operate in tech rather than construction, we leverage **lean principles** to streamline our software development processes and reduce inefficiencies-principles that align closely with lean construction methodologies. My role as a Senior Software Engineer emphasizes minimizing "waste" in code, processes, and resource allocation to enhance delivery speed and value creation.
One lean-inspired practice we've implemented is **continuous integration and delivery (CI/CD)** pipelines. By automating testing and deployment, we eliminated manual handoffs-similar to reducing overproduction or delays in construction projects. For instance, we reduced feature deployment times from weeks to just hours, increasing team productivity by 40% and delivering faster value to end users.
This approach fosters collaboration across engineering and product teams, much like lean construction's focus on synchronized workflows, driving consistent efficiency improvements.
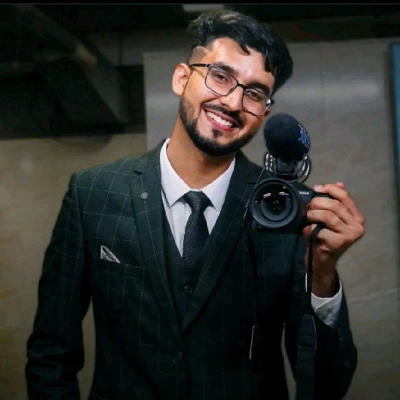