How Resilient and Disaster-Resistant Construction Influences Projects
Uncovering the secrets of resilient construction, this article delves into industry-shaping strategies and materials that withstand the test of nature. With contributions from leading experts, readers are offered a deep dive into the evolution of disaster-resistant building practices. Explore the expert perspectives on designing infrastructure, choosing durable materials, and storm-proofing homes that are shaping the future of construction.
- Designing Resilient Infrastructure
- Prioritizing Durable Roofing Materials
- Storm-Proofing Florida Homes
- Building with Stronger Materials
Designing Resilient Infrastructure
The growing focus on resilience and disaster-resistant construction has fundamentally changed how we design and build critical infrastructure. In my current work on a large-scale transmission line project with multiple substations across rural areas, we're constantly balancing the need for reliability with the challenges posed by wildfires, floods, and fire hazards—each of which carries significant risks. For wildfire resilience, our design began with a thorough assessment of surrounding vegetation and fire risk levels. We establish an Asset Protection Zone (APZ) around substations, ensuring a controlled buffer area where vegetation is managed to reduce fire intensity. This isn't just a one-time measure—it's part of an ongoing asset management strategy that includes scheduled vegetation clearing, firebreak maintenance, and continuous monitoring to minimize risk. Additionally, fire-resistant materials are incorporated into key structures, and substations are positioned strategically to limit exposure to high-risk zones. Another critical risk we address is fire hazards associated with oil-filled transformers, which can lead to catastrophic failures if not properly managed. To mitigate this, transformer compounds are designed with containment bunds to prevent oil spills from spreading and causing environmental contamination. These compounds are also isolated by fire-resistant walls to contain potential fires and prevent them from escalating into a larger disaster. Fire suppression systems and emergency response protocols are also integrated to provide rapid containment in case of an incident. Flooding is another major concern, particularly given the increasing frequency of extreme weather events. Our earthwork benches are designed to handle a 1% AEP flood event, meaning they can withstand conditions that statistically have a 1% chance of occurring in any given year. To prevent water buildup, we incorporate a 1.5% bench slope to direct runoff efficiently, alongside a well-engineered surface drainage system to move water away from structures quickly. In some areas, erosion-resistant materials and reinforced embankments provide additional stability, ensuring the long-term durability of the substations. Other resilience measures include regular inspections of drainage and containment systems, real-time weather and fire risk monitoring, and contingency planning for emergency access routes in case of extreme events.
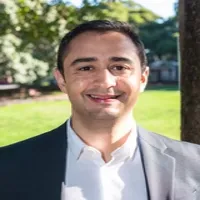
Prioritizing Durable Roofing Materials
The increasing focus on resilience and disaster-resistant construction has significantly influenced how we approach roofing projects at Toronto Roofer. We prioritize durable materials, advanced installation techniques, and weather-resistant designs to ensure longevity and safety, especially given Toronto's harsh winters and unpredictable storms.
One example of this is a recent commercial roofing project where we installed a reinforced TPO (thermoplastic polyolefin) roofing system. Given the client's concerns about heavy snowfall and high winds, we integrated a high-wind-rated fastening system, additional insulation for energy efficiency, and reinforced seams to prevent leaks. Additionally, we applied an ice and water shield to protect against ice dams, a common issue in the region.
By incorporating these disaster-resistant elements, we not only enhanced the roof's durability but also improved the building's overall energy efficiency and resilience against extreme weather conditions.
Storm-Proofing Florida Homes
We help Florida homeowners storm-proof their properties while lowering insurance costs. In our world, resilience isn't a buzzword--it's the difference between a home surviving a hurricane or getting torn apart.
So, we reinforce roofs like lives depend on it. Because they do. A standard shingle roof lasts maybe 15 years and peels off in 100 mph winds. We replace those with metal roofs rated for 150+ mph. They last 40 years and stay put even in Category 5 storms. That means fewer insurance claims, less damage, and homeowners who don't have to start from scratch after every major hurricane.
One Florida homeowner had their entire roof ripped off during a storm. We rebuilt with a fortified system--metal panels, reinforced decking, impact-resistant underlayment. The next storm hit with 140 mph winds. No leaks, no damage, no panic. That's the kind of difference real resilience makes.
Building with Stronger Materials
The increasing focus on resilience and disaster-resistant construction has led to prioritizing stronger materials, smarter design strategies, and adherence to stricter building codes. With extreme weather events becoming more frequent, incorporating features like impact-resistant windows, reinforced roofing, and elevated foundations has become essential.
One example is a recent new build in a flood-prone area, where we elevated the foundation above base flood elevation and used water-resistant materials for lower-level construction. We also integrated hurricane-rated windows and reinforced framing to withstand high winds. These features not only improved the home's durability but also reduced insurance costs and gave the homeowner peace of mind.